Сабельная пила из дрели – это возможно! Пила из шуруповерта
Автоматическая ножовка из шуруповерта
TOKARKA. В сюжете продемонстрирован процесс изготовления компактной автоматической механической пилы из шуруповерта. С помощью этого станка можно резать те материалы, что и простой ножовкой, но с высокой точностью и значительно быстрее. Если заготовка достаточно крупная, пока она разрезается, можно заниматься своей работой, не уделяя станку никакого внимания.
До того, как собирать пильный станок, мастер просмотрел огромное количество роликов на тему в Youtube, но не нашел ни одного видео по сборке. Вся конструкция — это авторская разработка, поскольку не видел ни одной механической пилы с вертикальным расположением маховика, только боковое.
О габаритах и весе судите сами: аппарат переносится с помощью одной руки. А парочку деталей узнает абсолютно каждый, кто хоть раз в жизни разбирал аккумуляторный шуруповерт. Абсолютно каждый самодельщик, у которого есть какой-то опыт работы, справится с изготовлением аппарата. Если сравнивать с таким режущим инструментом как болгарка, штуковина работает тихо. Во-вторых, она не разбрасывает пыль по всему помещению, а рез получается достаточно узкий, что экономит материал. С перерезкой вязких металлов или пластика не создается абсолютно никаких проблем. Тот, кто работал болгаркой по ним, отлично поймет. Аппарат можно использовать в полевых условиях, где нет электросети, если запитать от аккумулятора, любого подходящего. Например автомобильного или же от аккумулятора под шуруповёрт. Если со станочка снять тиски, можно перепиливать достаточно крупногабаритные объекты. Думаю, о том для чего нужна штука и как ее использовать, рассказал достаточно. Приступим к изготовлению.
Эта штуковина называется «мебельная направляющая», купить ее можно в различных магазинах мебельной фурнитуры или строительных супермаркетах. Для дальнейшей работы, ее необходимо аккуратно разобрать на части. Средняя выдвижная часть каталась на шариках, которые были вставлены в пластиковый сепаратор, они нам тоже пригодятся. По той причине, что направляющая не новая, она немножко была проржавевшей и решил ее слегка зачистить, так чтобы работать было приятно и выглядела всё получше. Две металлические части склеил с помощью эпоксидной смолы. Все отверстия, через которые она могла вытекать, аккуратно заклеил с помощью скотча. Внутрь заложил стеклоткань, хотя можно было бы заложить обычную х/б ткань.
Чтобы внутренние и наружные стальные части были хорошо центрованы между собой, в края вставил кусочки пластикового сепаратора с шариками и они точно выровнялись. Для повышения текучести эпоксидной смолы прогревал термофеном. Это электродвигатель постоянного тока, используются в аккумуляторных шуруповёртах. У него рабочее напряжение 12 вольт и несколько ампер тока. Вал вращается со скоростью 550 об/мин. Он не скоростной, зато у него крутящий момент большой. Деталь также от аккумуляторного шуруповёрта, называется она редуктором. В нем есть две ступени переключения скоростей, то есть нужны минимальные обороты и максимальный крутящий момент.
Два прикола — шатун и парочка игольчатых подшипников куплены в одном из интернет-магазинов. Так же запросто можно найти в различных сервисных центрах. Так выглядит редуктор планетарного типа изнутри, его вторая ступень выглядит точно так же как и эта. Понижение оборотов достигается за счет разницы передаточного числа от шестеренки на валу двигателя до шпинделя самого редуктора.Крышку, которая закрывала первую ступень редуктора, беспроблемно снял с проворотом и закрепил движок на два винта М4. И обратно всё вставляю. Решил провести небольшое испытание совместимости мотора и редуктора. Все работает идеально.
В пиле используется блок питания от компьютера. Сейчас движок подключен к 5 вольтам и 14 амперам. Для того, чтобы отделить пластиковый колпак, выкрутил два самореза, которые удерживали стальную шайбу. Здоровенная пружина — часть системы разобщения шпинделя от редуктора. Она не нужна. Под стальным кольцом, на которое давила пружина, находятся отвертстия, в них находятся по парочке стальных шариков. Самый простой способ заблокировать выскакивание — залить под них эпоксидную смолу. Но для того, чтобы она не затекла слишком глубоко и далеко, слегка подстывшая.Далее с 5 минуты
izobreteniya.net
Сабельная пила из дрели своими руками
Представьте, что вам необходимо отпилить деревянный брусок, а ножовки под рукой нет. Любимый электролобзик на другом объекте или вообще сломался, а рабочий процесс не терпит промедления. Ситуация знакомая многим, не правда ли? Большинство мастеров знают, как дорог рабочий инструмент в нужный момент. Работа кипит, проволочек нет, все довольны. Хуже, когда его нет, а заменить его попросту нечем. Самоделка, рассматриваемая сегодня заслуживает внимания хотя бы потому, что действительно помогает решить задачу распиловки с помощью обычной дрели или шуруповерта. Ее допустимо изготовить в домашних условиях своим руками. И это не какое-нибудь одноразовое приспособление. Это полноценный технический инструмент-насадка, который расширяет возможности основного электроприбора, предназначенного как нам казалось ранее, только для сверления и закручивания саморезов. С помощью нее вы действительно сможете распилить брусок или даже доску обычным полотном для ножовки по металлу и превратить обычную дрель в сабельную пилу. Давайте посмотрим, как это можно сделать.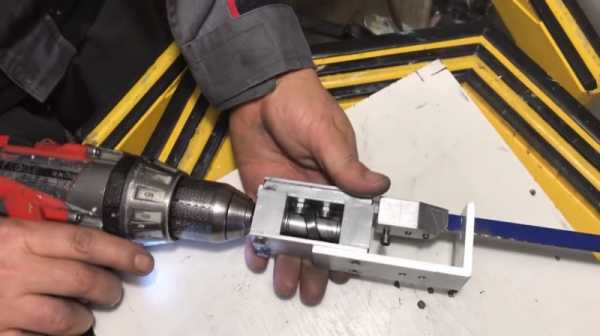
Принцип действия пилы
По сути, крутящий момент дрели никуда не девается. Он лишь преобразуется подобием фрикционной передачи в возвратно-поступательные движения за счет криво посаженного подшипника. Его корпус скользит между двумя мелкими подшипниками, установленными вертикально на небольшом металлическом квадрате. Именно этот элемент приводит в движение полотно, затянутое на его конце в специальный зажим. Насадка крепится на валу, проточенном для достаточного диаметра под патрон дрели или шуруповерта.Изготавливаем насадку для пиления древесины
Оговоримся сразу, что из подручных средств такое приспособление не собирается. Большая часть его достаточно точно выверена по размерам, проточена на токарном и фрезерном станках. Однако если вы сомневаетесь в возможностях своей мастерской, их всегда можно изготовить на заказ. Перед началом работ стоит сделать чертеж данной сборки, просчитав размеры каждого элемента и выверить их пропорционально. Наше приспособление сделано полностью из металла, и поэтому тиски в этот раз – инструмент обязательный.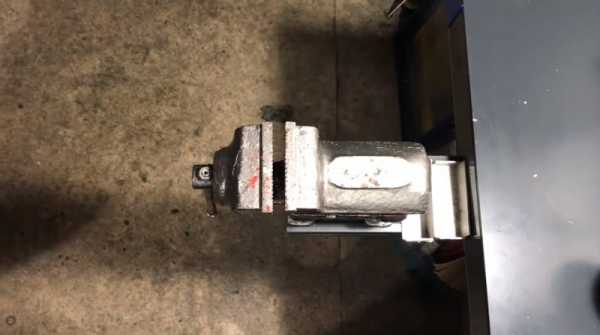
Делаем вал с подшипником
Для этого элемента необходим металлический стержень. Его сечение по возможности должно быть одинаковым, поэтому лучше всего если он будет проточенным на токарном станке.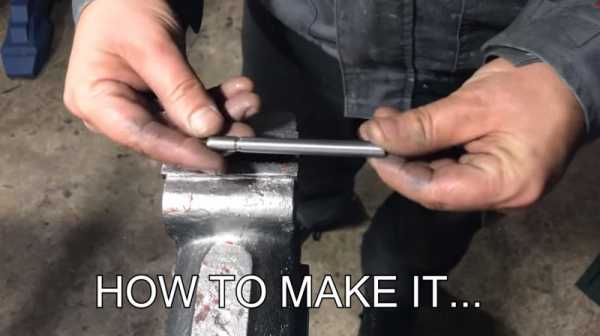
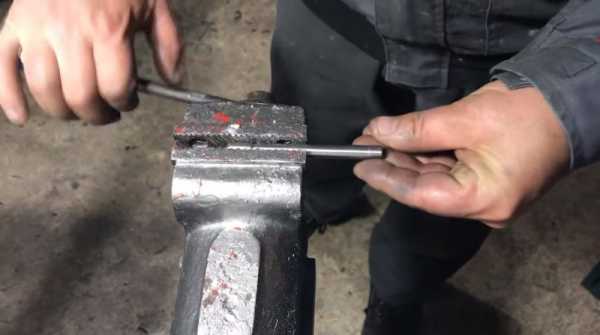
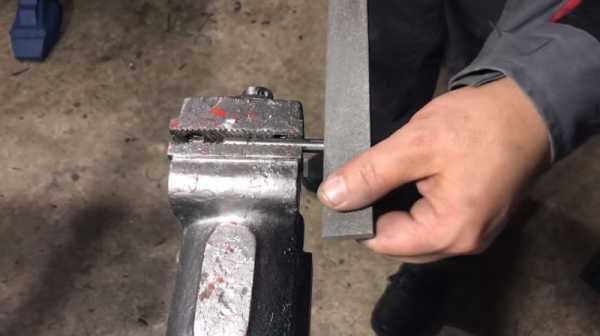
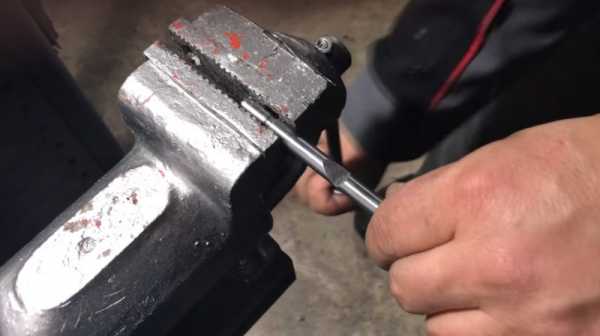
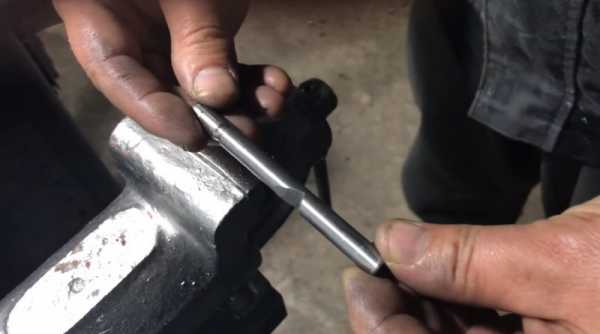

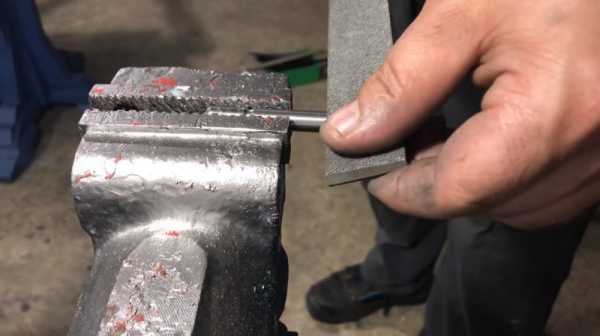
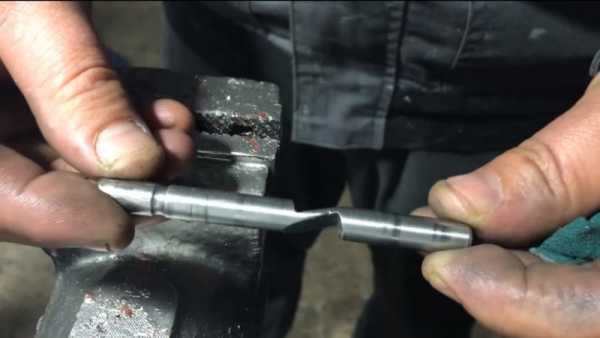
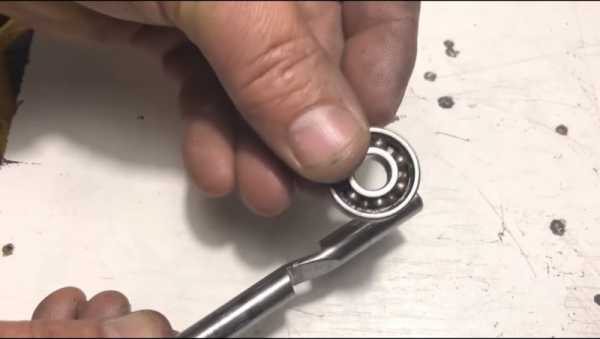
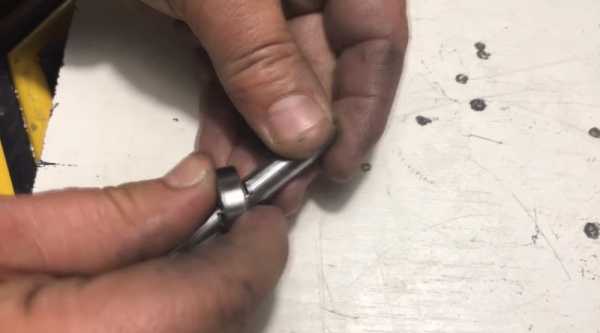
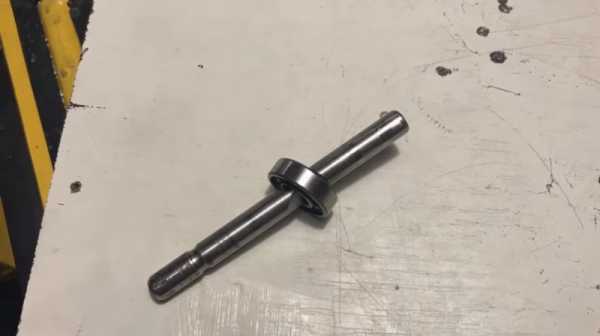
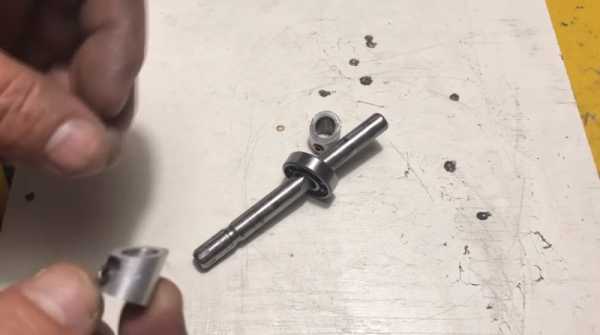
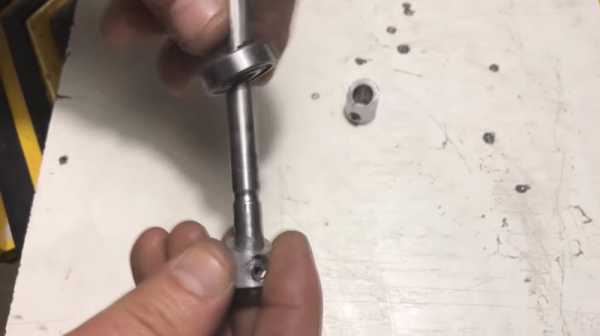
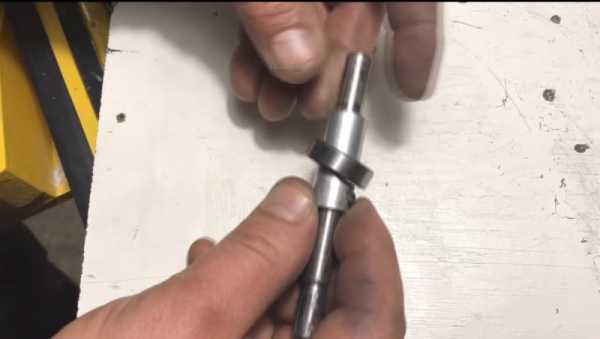
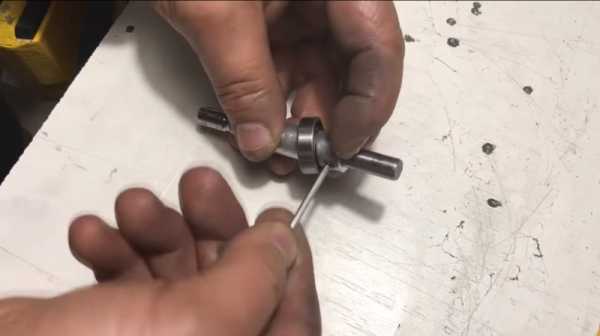
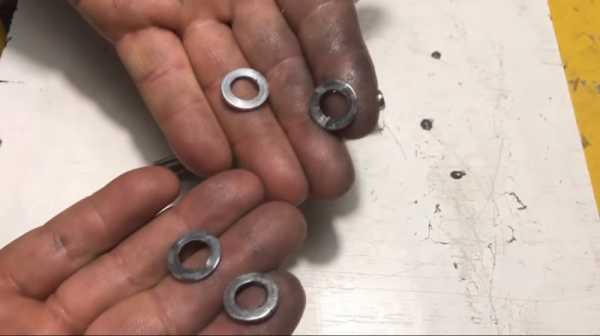
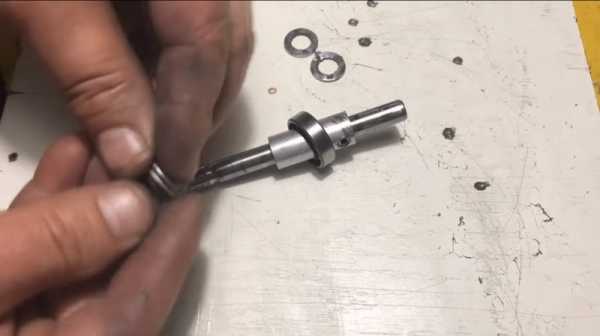
Оборудуем корпус нашего устройства
Наверняка все понимают, что сам по себе вал не будет работать в отдельности. Для него необходимы упоры, на которых он будет держаться, и относительно которых он будет двигаться. Они должны быть такими как на фото – два квадрата с отверстиями под свободный ход вала со стороны плоскостей, и крепежными отверстиями с резьбой под болты со стороны ребер. Собирается эта конструкция так (фото).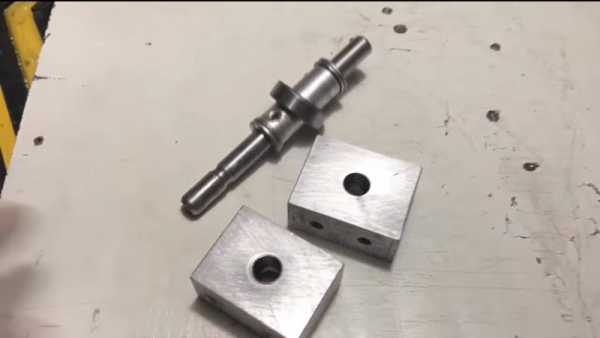
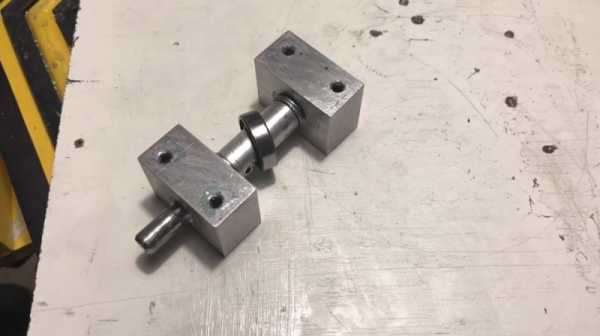
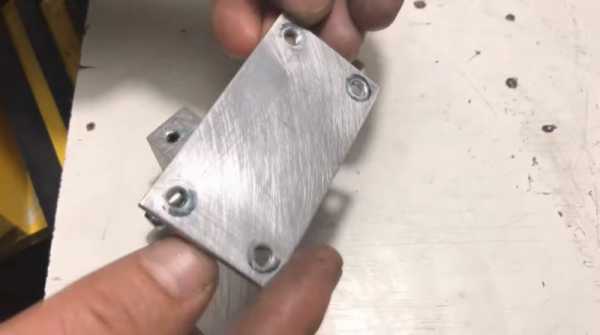
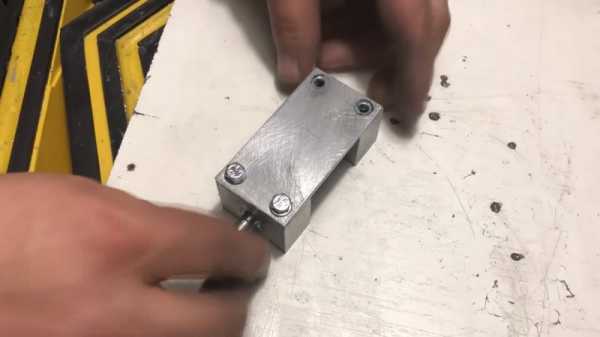
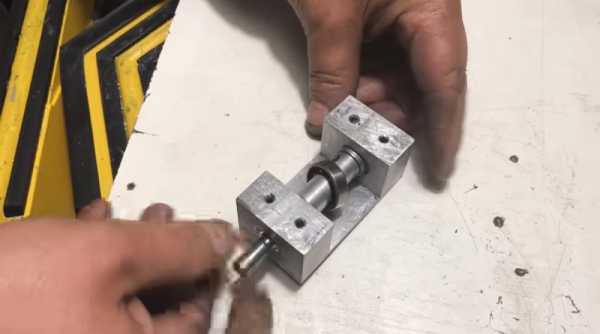
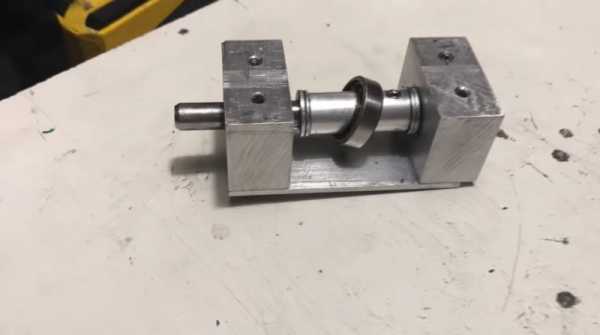
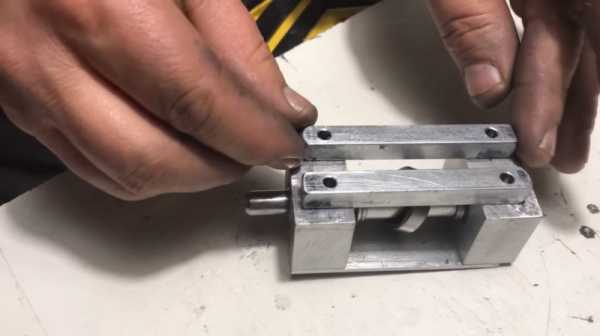
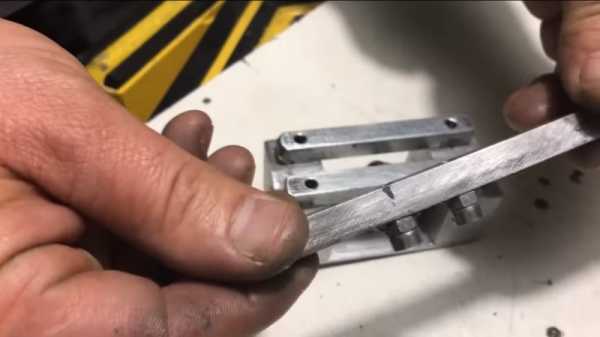
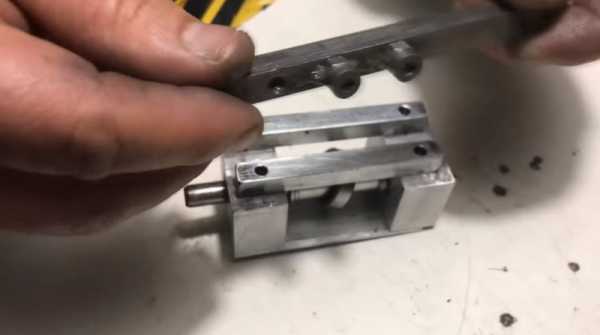
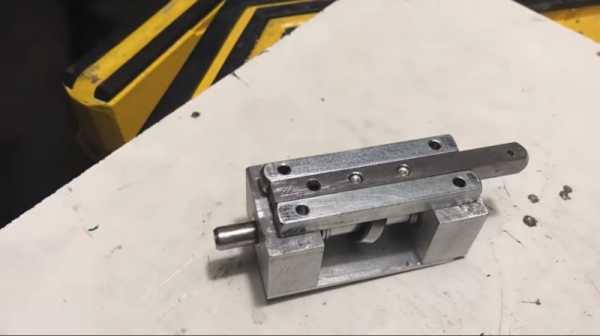
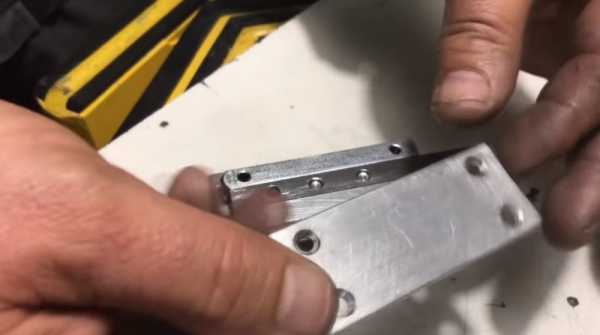
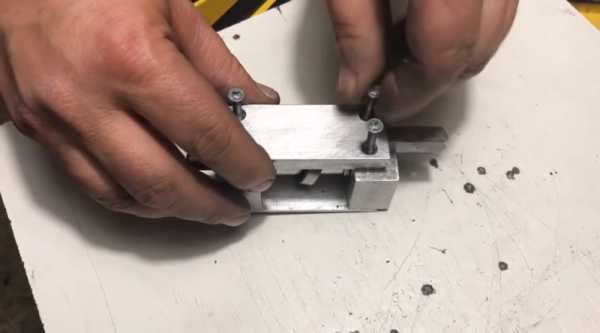
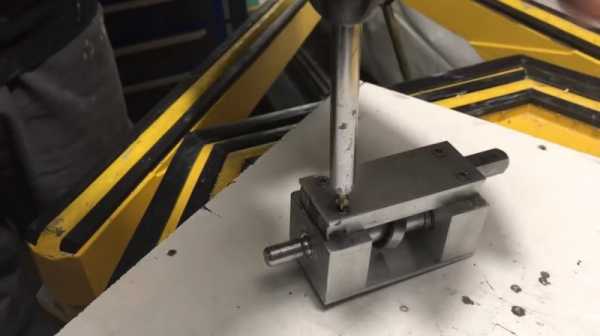
Изготавливаем наконечник для сабельной пилы
Для того чтобы закрепить ножовочное полотно необходим переходник-зажим. Наконечник, предложенный автором, имеет торцевой паз квадратного сечения. Со стороны плоскостей размещены прижимные болты под шестигранный ключ. При плотном зажиме они утапливаются заподлицо с плоскостью наконечника.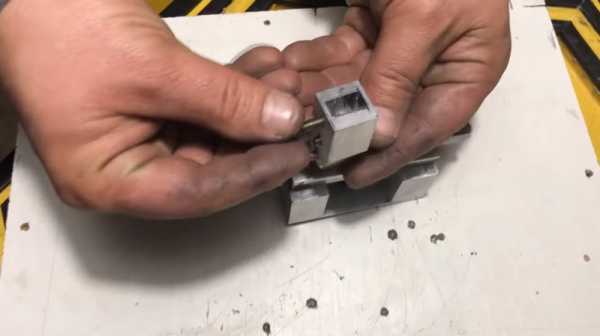
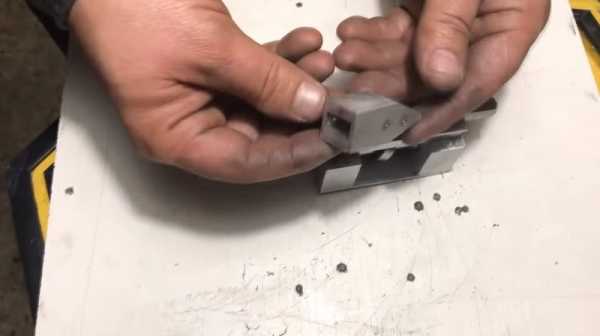
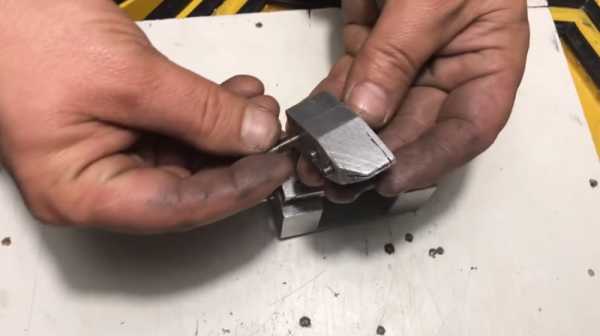
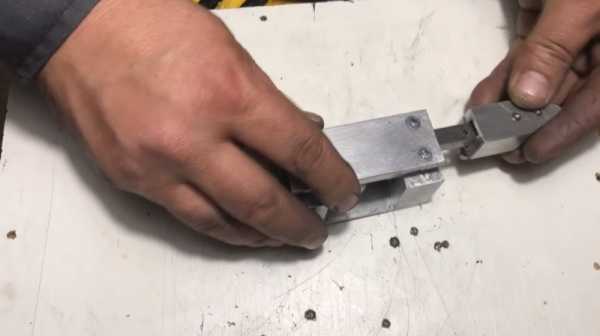
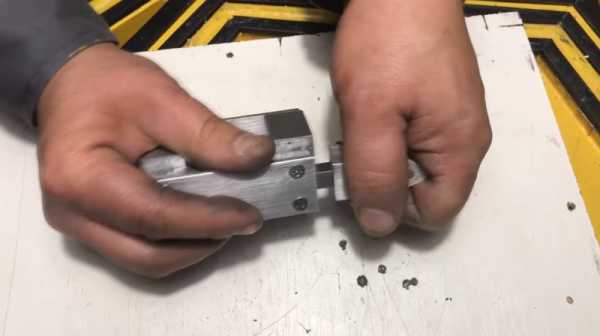
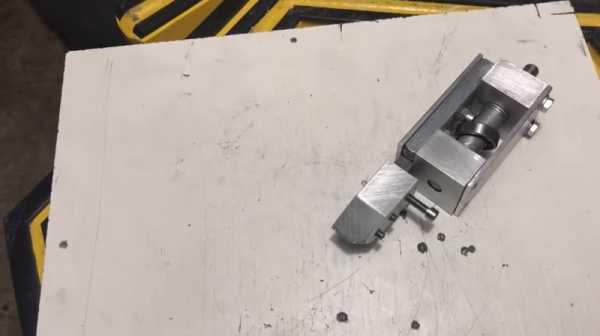
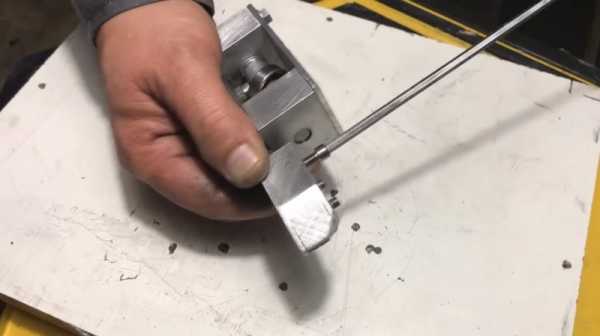
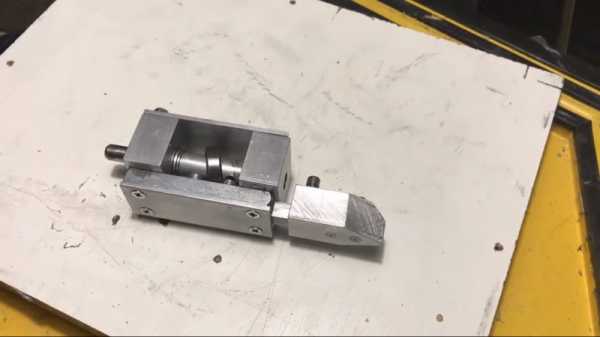
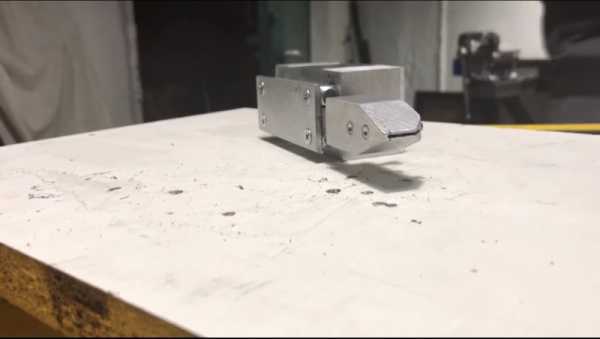
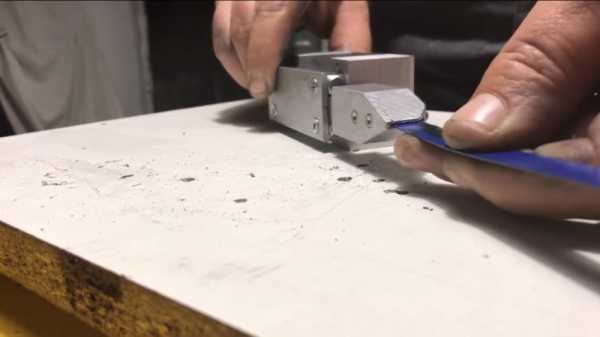
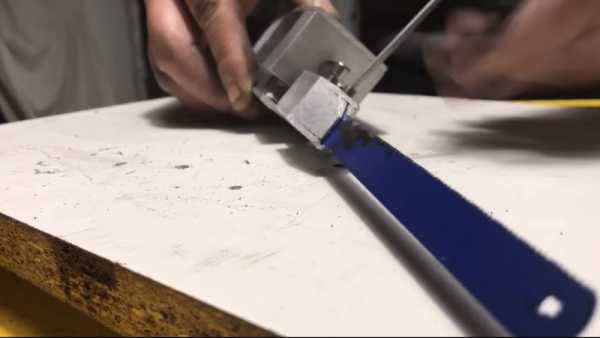
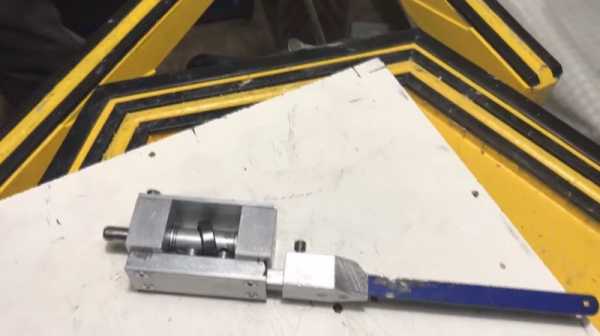
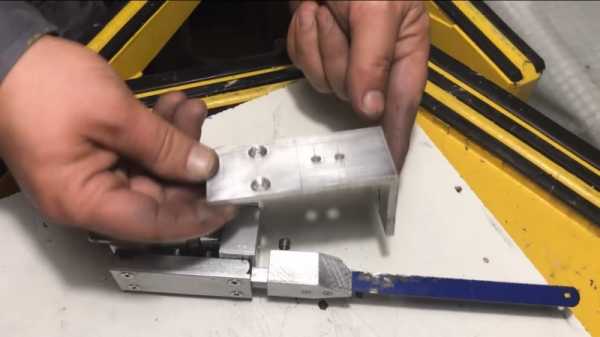
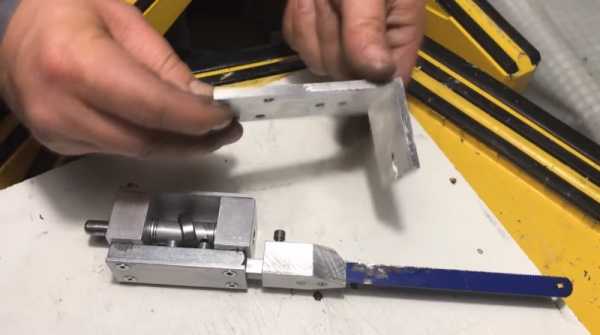
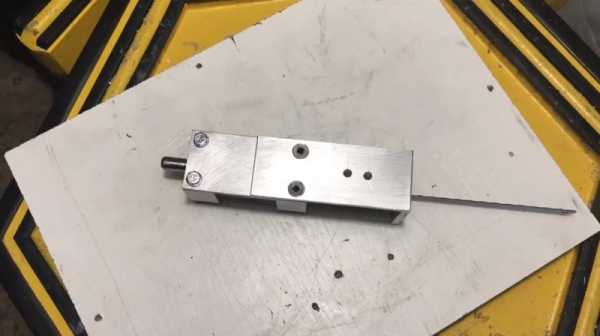
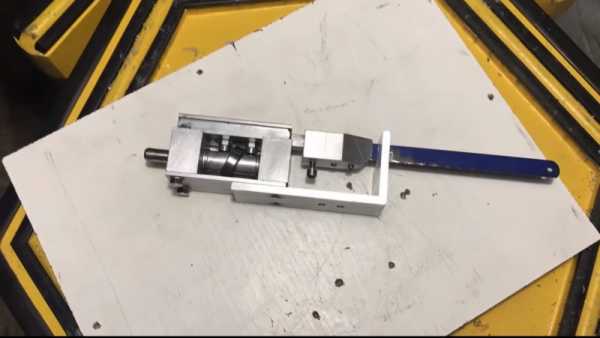
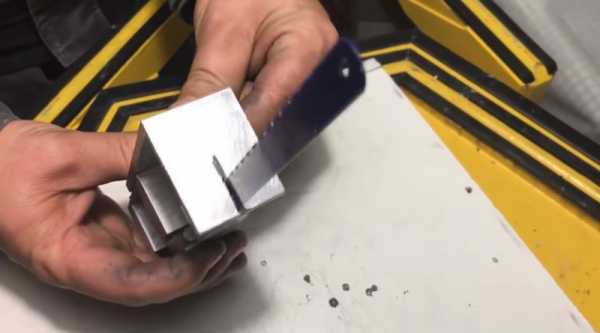
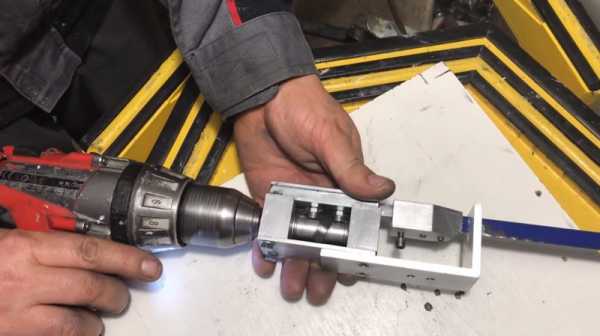
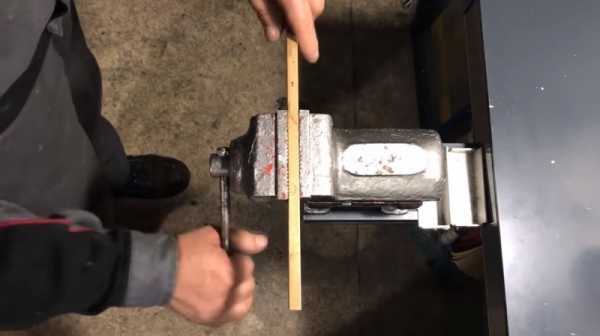
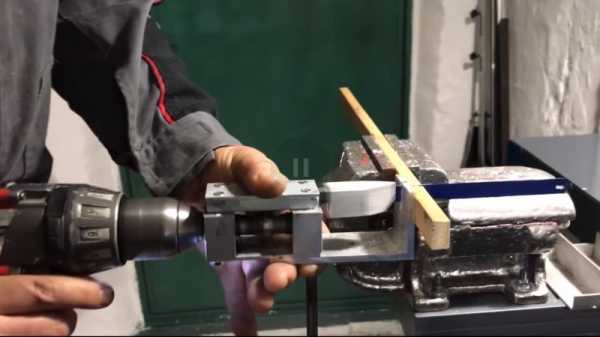
Смотрите видео
sdelaysam-svoimirukami.ru
КАК СДЕЛАТЬ МЕХАНИЧЕСКУЮ ПИЛУ ИЗ ШУРУПОВЕРТА | домашняя
Текст из видео:
- 00:00: Всем привет! В этом сюжете, я продемонстрирую, процесс изготовления, компактной, механической пилы. С помощью, этого станка, можно резать, все те же материалы, что и простой ножовкой, но, с высокой точностью, и значительно быстрее. Если заготовка, достаточно крупная, то в то время, пока она разрезается, можно заниматься, своей работой, не уделяя станку, никакого внимания. До того, как её собирать, я просмотрел, огромное колличество роликов, на эту тему в ютубе, но я не нашел, ни одного видео, по сборке. Вся эта конструкция,
- 00:31: это полностью, моя разработка, поскольку я не видел, ни одной механической пилы, с вертикальным, расположением маховика, было, только боковое. О габаритах и весе, судите сами. Мой аппарат переносится, с помощью, одной руки. А эту, парочку деталей, узнает, абсолютно каждый, кто, хоть раз в жизни, разбирал аккумуляторный шуруповерт. Короче говоря, абсолютно каждый самодельщик, у которого есть, хоть какой то, опыт работы, справится с изготовлением, этого аппарата. Если сравнивать, с таким режущим инструментом, как болгарка, эта штуковина, работает очень тихо,
- 01:02: во вторых, она не разбрасывает пыль, по всему помещению, а рез получается, достаточно узкий, что экономит материал. С перерезанием, вязких металлов, или пластиков, не создается абсолютно, никаких проблем. Тот, кто работал болгаркой, по ним, меня отлично поймет. Кстати, этот аппарат, можно запросто использовать в полевых условиях, там где нет электро-сети. Если запитать от аккумулятора, любого подходящего, на пример: автомобильного, или же от аккумулятора, под шуруповерт. Если со станка, снять тески,
- 01:51: можно перепиливать, достаточно крупно-габаритные объекты. Я думаю о том, для чего нужна эта штука, и как её использовать, я рассказал достаточно, теперь приступим, к изготовлению. Эта штука называется, мебельной направляющей. Купить её можно, в различных магазинах, мебельной фурнитуры, или же, в строительных супермаркетах. Для дальнейшей работы, её необходимо, аккуратно, разобрать на части. Средняя, выдвижная часть, каталась на шариках,
- 02:24: которые были вставлены, в пластиковый сепаратор они, нам тоже пригодятся. По той причине, что направляющая у меня не новая, она немного, была поржавевшей, и я решил, её слегка зачистить, так что бы, работать было приятно, и выглядело все, по лучше. Эти две, металлические части, я склеял, с помощью эпоксидной смолы. Все отверстия, через которые, она могла вытекать, я аккуратно заклеял, с помощью скотча. Внутрь, я заложил стекло-ткань, хотя можно было бы заложить,
- 02:54: обычную хебешную ткань. Для того что бы, внутренние и наружные, стальные части, были хорошо центрованы, между собой, в края я вставил, кусочки, пластикового сеппаратора с шариками, и они, точно выровнялись. Для повышения текучести, эпоксидной смолы, все это дело, я прогревал, с помощью термо-фена. Это, электро-двигатель постоянного тока, такие используются, в аккумуляторных шуруповертах, у него, рабочее напряжение 12 вольт, и несколько ампер тока. Его вал вращается,
- 03:24: со скоростью, 550 оборотов в минуту, он, не очень скоростной, зато у него крутящий момент, очень большой. Эта деталь, так же от аккумуляторного шуруповерта называется она, редуктором. В нем есть, две ступени переключения скоростей, то есть, мне нужны, минимальные обороты, и максимальный, крутящий момент. Эти два прикола, шатун, и парочку игольчатых подшипников, я купил, в одном из интернет-магазинов, так же, это запросто, можно купить, в различных, сервисных центрах. Так выглядит редуктор, планитарного типа изнутри, его вторая ступень, выглядит,
- 03:55: точно так же, как и эта. Понижение оборотов достигается, за счет разницы, передаточного числа, от шестеренки на валу двигателя, со шпинделя, самого редуктора. Крышку, которая закрывала, первую ступень редуктора, я безпроблемно снял с проворотом, и закрепил движок, на два винта М4, и теперь, обратно все вставляю. Я решил провести, небольшое испытание, совместимости, мотора и редуктора, все работает, идеально. Кстати, использую я блок питания, от компьютера. Сейчас движок подключен
- 04:25: к 5 вольтам, и 14 амперам. Для того что бы, отделить этот пластиковый колпак, я выкрутил, два самореза, которые в свою очередь, удерживали стальную шайбу. Эта здоровенная пружина, часть, системы разобщения, шпинделя от редуктора, она, как Вы сами понимаете, мне, абсолютно не нужна. Под стальным кольцом, на которая, давила пружина, находятся отверстия, в которых находятся в свою очередь, по парочке стальных шариков. Самый простой способ, заблокировать их выскакивание, это залить под них, эпоксидную смолу.
- 04:56: Но для того что бы, она не затекла, слишком глубоко и далеко, она у меня будет, слегка подстывшая. Пока эпоксидная смола, застывает в редукторе, я решил, заняться полезным делом. Я взял направляющую, закрепил её в тесках, и сверлю отверстия, в этих отверстиях, боковых, будут находиться винтики, которые будут притягивать, мотор редуктор, а через центральное отверстие, будет проходить шпиндель. Абсолютно все, сверлильные и фрезерные работы,
- 05:45: которые Вы увидите, в этом видео, выполняются, в моем самодельном, фрезерном станочке, который весит 10 кг. Фрезеровку я провожу, на внутренней стороне направляющей, сдесь будет находиться, пластиковая горловина редуктора. Эту всю работу, можно было бы выполнить, и с помощью, обычной бормашинки. Я примерял редуктор, и он стал идеально, хотя идеальная точность, сдесь не нужна, и всю эту сверлильную работу, можно было выполнить, с помощью обычной дрели, или же шуруповерта. Теперь пришло время, изготовить маховик,
- 06:17: он у меня будет сделан, из сантиметровой пластины текстолита. Токарный станок, в домашних условиях, очень облегчает жизнь, и ускоряет работу, но если бы у меня, его не было, то я бы нашел, альтернативный способ, как можно сделать, из квадратной пластины, круглую. Например, все острые углы, квадратной пластины, спиливаются, с помощью ножовки, после этого, делается отверстие, в центре, туда вставляется шпилька, с двумя гайками, пластина зажимается, и сама шпилька с заготовкой,
- 06:47: закрепляется в дрели. После этого, дрель включается, на небольшие обороты, желательно, что бы она была закреплена, на столе. Обточку можно производить, как напильником, так и куском наждака, наклеянным на деревянный брусок. А вот если в хозяйстве, есть такая штука, как ленто-шлифовальная машина, то это, можна сказать, победа, по той причине, что работа ускоряется, в несколько десятков раз. Достаточно, дрель к ней поднести, и аккуратно и плавно, сошлифовывать все, острые грани. Кто хочет, тот ищет возможности, кто не хочет, ищет оправдания.
- 07:18: Для изготовления, резьбовой втулки, я взял, латунный шестигранник, и по его центру, сверлю отверстие. Через эту штуку, будет передаваться, энергия вращения, от редуктора к маховику. Теперь я открою Вам,
- 08:03: супер-секретную информацию. Дело в том что, без этой резьбовой втулки, вообще, можно обойтись, её можно заменить, обычной гайкой. А вот так вот делать, я очень не советую. Дело в том что, если заготовка, вырвется во время обработки, она может прилететь, прямо в голову, и разбить её. Эта заготовка, то же из того же самого, текстолита,
- 09:21: из нее будет сделан, фиксатор подшипника. Диамметр отверстия, я расточил
- 09:52: на пару соток больше, чем диамметр, самого подшипника, и он туда свободно, залазить не хотел, но мне его, удалось вставить, приложив, достаточно большое усилие. Для изготовления, такого держателя подшипника, подойдет, абсолютно любой пластик, который имеет, хорошую стойкость, к динамическим нагрузкам. Например, идеально подойдет, стекло-текстолит, а так же капралон. Теперь я продемонстрирую, как можно сделать, шестигранное отверстие, без специальных станков и инструментов. Теперь латунный переходник,
- 10:22: я разогрею до градусов 50, 60. При нагревании, текучесть эпоксидной смолы, сильно возрастает, и она затекает, абсолютно, во все щели, но стоит не забывать о том что, при сильном перегреве, она застынет за пару минут потому, слишком сильно нагревать, металлический объект, нельзя. После заливания, всю эту штуковину, я поместил, в одно теплое место, и через час, смола полностью отвердела. После этого, я латунную вставку,
- 10:54: нагрел, с помощью электрического паяльника, до 100 градусов. При нагревании, все материалы расширяются, и латунная вставка, не исключение. После того, как она остыла, с помощью, рукоятки шила, я смог свободно её вытолкнуть, из отверстия. На этих, двух саморезах, удерживается редуктор, но дело в том что, они выпирают, и мешают мне, нормально закрепить, держатель подшипника. Что бы избавиться, от этой проблемы, шляпки на них, я превратил, в потайные. Отверстия, куда будут закручиваться,
- 11:27: эти уже, потайные саморезы, я тоже осверлил, таким образом, что бы шляпка, полностью пряталась. Сейчас я работаю, 4мм. сверлом, и через эти отверстия, будет закрепляться, держатель подшипника. Теперь уже, через имеющиеся отверстия, я сверлю, его самого, удерживается на направляющей он, с помощью супер-клея. В этом отверстии, на маховике, будет закрепляться ось. Этот шатун, я купил,
- 12:06: в том же самом магазине, где купил редуктор и двигатель. Он предназначается, для ударных дрелей, если я, не ошибаюсь. Он выполнен, из очень высоко-качественного, прочного пластика. Ради аккуратного, внешнего вида, я решил его, немного облагородить, с помощью фрезера, хотя это, конечно же, можно было, и не делать. Шатун, полностью готов,
- 12:51: и я приступил, к изготовлению оси, она будет иметь, резьбовую часть, в маховик, она будет закручиваться. Энергия, будет передаваться, не напрямую, а через вот этот вот, игольчатый подшипник. Правда, у меня продвинутый, плашко-держатель? Самый лучший, источник питания,
- 14:22: для мег-пилы, это конечно же, аккумулятор, но мне, он будет не удобен, потому, я буду использовать, свой блок питания, от компьютера. Я установил выключатель, и светодиод, который светится, во время работы, а так же, на лазерном гравере, я сделал табличку, на которой указано, напряжение, и ток. На задней стороне, у него находится, два сетевых разьема, один из которых, я переделал. Все дело в том что, провод, который, я только что, выдергнул, способен запитывать у меня, несколько аппаратов. На пример: фрезерный станок,
- 14:52: мини-сверлильный станок, микро-плиту, то есть это, очень удобно, нет, целой кучи проводов, один провод, все запитывает. Направляющую, я закрепил, на координатном столике, и фрезерую канал. Его кстати, можно сделать, с помощью болгарки, а края подровнять, с помощью напильника. Подвижной части, я закрепил, две резьбовые втулки, через которые проходят, два винта М4. В данный момент, бигунок удерживается, в направляющей, за счет пластикового сепаратора,
- 15:22: с парочкой шариков, с каждой стороны, от него. Сам по себе бигунок, был изготовлен, точно так же, как и направляющая, то есть, я его заполнил стекло-тканью, и залил все это дело, эпоксидной смолой. Площадка, на которой закреплена ось, сделана, из дюраллюминиевой пластинки. Сама по себе ось, это трубочка, из резьбой внутри. Наступило время, изготовить боковые пластины.
- 16:29: Для того, что бы их сделать, я взял, два отрезка, дюраллюминиевой полосы, и склеял их, на супер-клей. Закрепил в тесках, и делаю фрезеровку, все это надо, для хорошей точности. До того, как я изготовил, этот фрезерный станочек, такую работу, я выполнял, с помощью напильника, и мне удавалось, достичь точности, пары соток миллиметра. На корпусе редуктора, и на крышке, к которой, я закрепил двигатель, есть специальные выступы,
- 16:59: по два, с каждой стороны, так вот под них, я теперь фрезерую места. Места я выдалбливаю, достаточно с большим запасом, это по той причине, что потом, они будут заполнены, эпоксидной смолой. После того, как она застынет, до не текучего состояния, я аккуратно, эти бочины, одену, на крепежные места, и все это дело, стяну. Надо это для того, что бы двигатель, не болтался, по отношению к редуктору. Если всего, этого не сделать, то будет происходить, достаточно быстрый, и сильный износ, подвижных частей редуктора, и шестерней на двигателе.
- 17:31: Эти две, текстолитовые пластины, я сначала, вырезал ножовкой. После этого склеял, и все тщательно выровнял, во фрезерном станке, и теперь, я Вам продемонстрирую, супер-пупер фокус, как обычным сверлом, сделать, огромное отверстие. Каждый, из этих пластин, будет находиться, по подшипнику, и в них , будет находиться, шарнир откидывания, всей пилы, надо эти подшипники, для плавного, и мягкого хода, а так же, для точности. Все эти извращения, нужны по той, простой причине что расточной резец, под этот патрон,
- 18:01: оказался, слишком коротким. Под один из кулачков, я заложил пластины, и вся заготовка, сместилась. Теперь, центр отверстия, будет ближе, к центру, самой заготовки. Дассес-фастантишен! Я-Я! После, смазки вазелином,
- 18:39: запихуевомость, резко возростет. Это приспособление, я собрал, не за долго, после покупки, токарного станка, и я им, очень доволен, хотя оно примитивное, но работает отлично. Самое большое, его достоинство, состоит в том, что оно очень быстро, заменяется, вместо резцодержателя. У меня есть, разточной резец, но, для его установки, пришлось бы, выкручивать, четыре болта, а потом их, закручивать обратно, а так, я выкручиваю, и закручиваю, только лишь, фиксатор, резцодержателя. Правда, не хилая дыреха получилась,
- 19:10: от такого, сверлышка? Кстати, делать и сверлить, это не одно и то же, и про сверление, я ничего не говорил. Через эти отверстия, будут проходить, крепежные болты, а в сами пластины, будут упираться, резьбовые втулки. Фиксатор подшипника, я приклеял, с помощью, супер-клея, и через уже, имеющиеся отверстия, сверлю снова. Это, один из болтиков, на которые, будут закручиваться, между собой, бочины стойки, в который, будет находиться, мотор-редуктор, но он, слишком длинный,
- 19:41: у меня было, два варианта, как его укоротить, болгаркой подрезать, и надышаться пыли, или же, срезать в токарном станке, я выбрал, токарный станок. Не расточенными кулачками, нельзя браться, за резьбу болтика, если Вы, конечно собираетесь, им, еще пользоваться, потому, я нашел гаечку, а вторая сторона болта, там где шляпка, упирается в кулачки, и не провернется. На рынке я купил, целую кучю,
- 20:19: вот таких вот, стальных трубок. Они завальцованные, с каждой стороны. Я эту, немного отжег, то есть, нагрел до красна, и дал спокойно остыть, она у меня пойдет, на резьбовые втулки. Благодаря вот такой вот, маленькой хитрости,
- 21:10: я загнал, все три, резьбовые втулки, до одинаковой длины. Супорт, я зафиксировал, на ходовом винте, а резец к трубке, придвигал, только с помощью, маленького, продольного супорта. После того, как первую трубку, я подогнал, до нужной длины, две остальные трубочки, я вставлял, в патрон, с опорой на стержень, но уже не трогал, продольный супорт. Вот и дошла, очередь до шарнира, он у меня тоже, будет сделан, из латуни. То место, которое я сейчас, протачиваю,
- 21:40: будет служить, для посадки подшипника, с другой, стороны болванки, будет проточено, точно такое же. Судьба, этой штуковины, сложилась, таким образом, что она, успела побывать, пушкой-гаубицей. Теперь, с помощью моей, самодельной баляринки, я обдалбываю, квадрат дюрали 30 на 30мм.
- 22:10: Это, будет площадка, на которой, будет, закреплен шарнир, на пару винтиков М4. Площадку, я немного облагородил, напильником, просверлил, парочку отверстий, сделал резьбу, и закрутил туда, винтики. Все ходит, достаточно плотно, но плавно, это то что мне, нужно было. Я забыл, снять на видео,
- 22:40: то, как я залил, эпоксидную смолу, которая находится, вокруг горловины редуктора. Я сделал, специальную опалубку, из стекло-текстолита, миллиметрового, выложил её, закрепил на супер-клей, и залил туда. Винты, держателя-подшипника, возле, шпинделя-редуктора, заходят не в гайки, а в специальные, резьбовые втулки, которые я вставил, для того, что бы их, не залила эпоксидная смола, и винты, можно было, выкручивать. Платформу, я закрепил в тесках, и делаю отверстия, меньшего диамметра. Я его, чуть позже, расверлю, под резьбу М5. Резьбу я нарезал, точно так же,
- 23:18: как я, уже показывал. На счет дюрали, есть один, серьезный ньюанс. Этот металл, достаточно вязкий, и когда Вы, нарезаете резьбу, не нужно, жалеть смазку. Это, профильная труба, изготовленна, из современного, аллюминиевого, твердого сплава. Она очень хорошо, по этой причине, обрабатывается, гораздо лучше, чем, простой дюраль. Купил я её, и много другого аллюминия, в одной из фирм, которую я нашел, через интернет, так же их, можно найти, в различных, строительных супер-маркетах. Стоят, такие изделия, конечно же, не дешего, но с учетом того, на сколько у них,
- 23:49: точная геомметрия, хорошая чистота поверхности, и имеется так же, защитное покрытие, я считаю, эта цена, вполне оправдана. До того, как приклеять, площадку к платформе, на супер-клей, я её выставил, по штанген-цыркулю, то есть, очень точно, и теперь, с помощью сверла, делаю отметки, на которых, сделаю кернение, и произведу, сверление. Это, дюралевый круглячок, от него, я отрежу две шайбы,
- 24:20: они, будут вставляться, в трубу-платформу. Для чего они нужны, я обьясню позже. Эх, жаль что у меня, нету мег-пилы! Туда-сюда обратно, резцом, и о Боже, как приятно резать, вязкие металлы, правда идет, большая потеря, материала. Эти вставки, я так же выточил,
- 25:19: с очень, высокой точностью. Нужны они, для того что бы, при затягивании, винтов крепления, площадки, последнее, не продавило трубу, и не деформировало её. Это, двух-миллиметровый, дюралевый уголок, конечно же, не самое лучшее решение, по скольку, я хотел бы конечно, по толще найти, но у меня, не нашлось, другого, и потому, я отрезал этот. Одной стороной, этот уголок,
- 25:49: будет прикручен, к бегунку, а вот, в другой, его стороне, будет закреплена, эта же ножовка, которой я, сейчас режу. Я все по закреплял, на свои места, и решил провести, первое испытание. Первое, что я не учел, это то что, на пиле, имеется скос, от рамки, до полотна, и её сильно колбасило, вверх-вниз. В ножовке, было закреплено, полотно по металлу, и срез получился, весьма чистый, и ровный. Я решил, немного побаловаться, и посмотреть, будет ли, такой чистый срез,
- 26:19: во второй раз, все повторилось на 100%. Во время работы, пила достаточно сильно, вибрировала, и я решил сделать, вот такие вот, специальные подставки, под платформу. Они нужны, для гашения вибрации, и что бы она, не скакала по столу. Сделал я их, из этого, аллюминиевого профиля, его обычно, цепляют на ступеньки, что бы они, не были скользкими. Тест я проводил, со вставленным, рабочим подшипником, продольного скольжения, у него, стальной сепаратор, и большое, колличество шариков, он дает, отличную жесткость.
- 26:49: Для того, что бы соосность, бегунка и уголка, были 100%, их я склеял, на супер-клей, и только, после этого, сверлил. В ножовке, я так же высверлил, парочку отверстий, правда прийдется, еще одну сделать, для анулирования, подскоков, во время движения, из-за скоса. В любом, аккумуляторном шуруповерте, установлена, такая вот кнопка, благодаря ей, можно плавно, регулировать, скорость оборотов. Я думаю, эта кнопка, мне идеально подойдет, по скольку мой, блок питания, выдает 12 вольт, и 9 ампер тока. Блок переключателя, полярности,
- 27:21: сидел, на двух защелках, их я отщелкнул, с помощью шила, он мне, не нужен. С той целью, что бы кнопка останавливалась, в нужном, мне положении, я решил, её немного, доработать. На конце винтика, с накаткой, у меня одета, резьбовая втулка, и я её, немного проточил, в токарном станке, а на винтике, я сделаю, шлиц под отвертку. Под отвертку, я сделал отверстие.
- 28:17: Принцип, работы выключателя, я не буду обьяснять, по скольку это, и так понятно, а вот транзистер, я закрепил, прямо, к аллюминиевой стенке. Аллюминий, отлично рассеивает тепло, и он, никогда не перегреется. Теперь, дошла очередь, до последнего, элемента конструкции, это конечно же, крепежик тесков. Благодаря, этой штуковине, тески, закрепляются на платформе, и могут, передвигаться. В одной из полосок, будут сделаны отверстия, в которых, будет нарезана резьба, под винты М4, и они, будут стягиваться, между собой.
- 28:47: Если эти винты, будут затянуты, не очень плотно, то тески, можно будет, свободно перемещать, по платформе. У меня получилось, все сделать точно, и эта штуковина, ходит практически, без люфта, хотя винты, достаточно сильно, ослаблены. Если мне понадобится, эту штуку, часто передвигать я в бочине, просто сделаю, парочку отверстий, куда размещу, парочку винтов, с накаткой, на шляпке. Это, все не обходимо, для того что бы, полотно, можно было вырабатывать, на 100%. Хотя конечно же, есть способ, и по проще,
- 29:17: это просто, переставить полотно, не выработанной стороной, к тескам. Единственные, свободные тески, которые, мне удалось, найти у себя, это ТБУ-45, их я и буду, использовать. Они достаточно узкие, что бы разместиться, и достаточно, прочные. На обеих, половинках тесков, имеются, резьбовые отверстия, для крепежных винтиков, потому, конечно же, их можно, размещать по разному. С помощью, штанген-цыркуля, я сделал, очень точную разметку, под те места, где должно быть, отверстие, под крепежные винтики.
- 29:47: Фиксатор тесков, я достаточно жестко, закрепил на месте. Вы наверное, отлично видите, на сколько, подскакивает направляющая, это по той причине, что в ножовке, я не сделал отверстие, для анулирования подброса. Испытания, которые я сейчас провожу, не обходимы для того, что бы я мог, найти недостатки, и рассказать, Вам о них. Первое, на что я, обратил внимание,
- 30:18: это то что, мег-пила создает вибрацию, все это из-за того что, ножовка достаточно тяжелая. Она очень классного качества, и очень, хорошо подходит, для ручной работы, но в мег-пиле, она слишком тяжелая. Хотя, ради справедливости, надо, отметить тот факт, что вибрация, это, характерная особенность, подобных устройств, вспомните, хотя бы тот же, электро-лобзик. По этой причине, полностью, избавиться от вибрации, подобного, рода устройствах, просто не возможно, её можно, сильно снизить, на пример, установив, очень легкую ножовку.
- 30:48: Срез получается, достаточно чистым, и ровным. Как Вы видите, я отрезал, кусочек, букового бруска, толщиной, меньше чем спичка. Я решил, перерезать, что нибудь по серьезней, чем дощечка. В тесках я закрепил, в дюраллюминиевый кругляк, диамметром 50мм. Дюраль, штука очень вязкая, потому, я добавляю, немного масла. После того, как я отснял, весь видео-материал, для этого сюжета, я занялся монтажом. И пока я, монтировал видео, я решил попробовать, на сколько хорошо,
- 31:18: эту же заготовку, перепилит, полотно по дереву, и я, просто обалдел, перепилить удалось, раза в полтора, быстрее, при том, без масла. Во время перерезания, этого кругляка, я его переодически, трогал рукой, с той целью, что бы проверить, на сколько сильно, он нагрелся. Как выяснилось, он практически, не нагревался, и был, еле теплый. К тому же, если был бы, сильный нагрев, то масло бы, дымило, и Вы бы это, увидели. Обратите внимание, на сколько тонкий срез. Если бы, я делал срезание, в токарном станке, то в стружку ушло бы, очень много материала,
- 31:49: хотя, в моем Корвете 401, это сделать, было бы, просто не возможно. Я считаю, что после полной отладки, этого станочка, можно будет, скорость срезания, поднять, раза в два-три. Я решил, что Вам, будет интересно посмотреть, как процесс работы, мег-пилы, выглядел для меня. Камеру, я снял со штатива, и решил, немного поснимать с рук. Платформа мег-пилы на столике, закреплена, с помощью, пружинного зажима. Я нашел, еще один, из не достатков. Как выяснилось, хоть тески, и были новые,
- 32:20: но они были, достаточно кривые, посмотрите, на сколько они, сейчас раскарячились. Хотя, если немного подумать, над их названием, то все, становится понятно. ТБУ расшифровывается, как тески бытовые, универсальные, и они, совсем не предназначенны, для таких работ, сдесь место, станочным тескам. Боковые пластины стойки, в верхней части, были стянуты, с помощью, резьбовых шпилек М4. Свободное отверстие, в нижней части, боковых пластин, мне скорее всего, пригодится, для кое-каких целей. Кстати, еще об одном не достатке,
- 32:51: направляющая, в том месте, где я, выфрезеровал паз, оказалась ослабленной, и её нужно будет, немного усилить. На счет стойки, шарнирного узла, у меня не возникло, абсолютно никаких нареканий. С платформой, тоже все в порядке. Пару слов, на счет ножек, они у меня сделаны, из слишком твердой резины, делать их желательно, из мягкой, что бы, гасилась вибрация. На счет платформы, меня посетила, довольно, интересная мысль, Дело в том что, это дюралевая, профильная труба, и я посчитал, на калькуляторе,
- 33:21: там можно, разместить свободно, 90 полотен, под ножовку. Теперь, пару слов, на счет питания. Сейчас пила подключена, к 12 вольтовому разьему, на 9 ампер, и работает, отлично. Скорость выставлена, за счет кнопки. К этому блоку питания, я хочу сделать, кстати, свою отдельную кнопочку, с регулировкой, чтоб можно было, запитывать, различные, другие устройства. Кстати, сам блок питания, я хочу отправить, на ПМЖ, в какое то, удобное место. Вы сами себе представляете, сколько, интересных устройств, можно сделать, на базе движков, под шуруповерты.
- 33:51: Пока пила, по тихоньку, грызла кругляк, я занимался, своими делами, баловался с камерой, общался с женой, ну в общем, очень удобно, то что можно, делать что хочешь, пока она, сама по себе, работает. Ну, и как вариант, не делать вообще ничего, попросту говоря, пуй пинать. Когда, я буду проводить, работу, по исправлению огрех, этой конструкции, я обязательно, поставлю утяжелитель, он позволит, повысить нагрузку, на полотно, и зубцы, будут гораздо глубже, вгрызаться в материал,
- 34:21: в следствии чего, скорость разрезания, повысится. Если бы, я кругляк в тесках, провернул на бок, хотя бы один раз, то скорость, то же, очень сильно, возросла бы. Срез получился, достаточно ровный. На ощупь рельеф, практически не чувствовался. Я думаю, нет резона, говорить о том, что в ручную, так отрезать, никогда бы в жизни, не получилось. Пруток разрезался, значительно бодрее, сталь, не на столько вязкая, и более твердая, во вторых, площадь контакта, с полотном, гораздо меньше. О чистоте среза, судите сами.
- 34:59: Такой, аллюминиевый профиль, часто, цепляют на ступеньки, в него, вставляется резинка. Нужен он, для того что бы, обувь не скользила. Он изготовлен, из очень твердого, закаленного дюраля, но после, выполнения реза, я не нашел, ни одного, обломанного зуба. Одно, из больших достоинств, работы, такого станочка, состоит в том что, движение ножовки, абсолютно линейна, и вероятность, поломки полотна, нулевая. Ради того, что бы посмотреть, как работает пила,
- 35:34: я решил, отпелить еще один, кусочек квадрата, Если бы, это нужно было, делать вручную, я бы в жизни, так прикалываться, не стал. Тески, я кстати передвинул, к средине платформы, я думаю, это видно, потому, что на полотне, сохранилась краска. Во время разрезания, этого гипсового бруска,
- 36:09: я слегка надавливал, на конец направляющей, и выявился, еще один, недостаток. Дело в том что, полотно уводило, в сторону, не слишком на много, но все таки уводило, мне такое, конечно же, не надо. О том что, такая проблема может быть, я то же знал, я видел, что уголок, к которому, я прикручивал ножовку, был слишком слабый. Правда, эта проблема, очень легко устранима. Есть, довольно хорошая поговорка, на эту тему, о сознании, причины проблемы, это, половина её решения, потому, никогда не расстраивайтесь,
- 36:39: если Ваш, самодельный станочек, не работает так, как Вы задумывали, изначально, просто, найдите проблему, и решите её. Так выглядит срез, выполненный, полотном по дереву. После, исправления всех огрех, механническая пила, будет работать идеально, я в этом, уверен. Все, крупные производители, какого либо, оборудования, прежде, чем запустить, свой товар, в серийное производство, производят испытания, и доработки. Эта, механническая пила, и фрезерный станочек, были изготовлены, на этом, журнальном столике,
- 37:10: Благодарю всех, за внимание! ВСЕМ УДАЧИ!!!
postila.ru